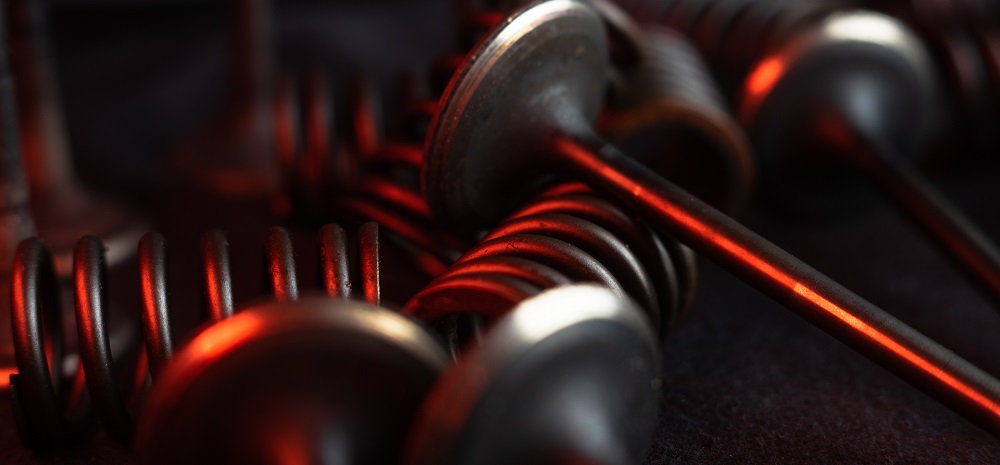
Coating Devices of Liquid Materials and Applicators of Liquid Gaskets
Since liquid gaskets involve a great number of varieties with respect to their applications, such as the organic solvent base, aqueous base, anaerobic base, and silicone base, it is necessary to design the coating device in full consideration of properties of these viscous fluids.
Cost savings and improved sealing properties associated with the application of liquid gasket provide irresistible attraction, and many gasket users are urgently demanding the development of coating devices. In response to these requests, ThreeBond, who has been studying the coating technologies for the past 60 years as a global manufacturer of liquid gasket material, is offering up a solution to our customers for coating devices of liquid materials.
Ultimately, ThreeBond offers various types of coating devices for liquid gaskets to ensure you have what you need for every type of application. Our R&D team is hard at work continually refining our solutions to ensure they provide you with the highest quality product that saves you time and money.
Cost savings and improved sealing properties associated with the application of liquid gasket provide irresistible attraction, and many gasket users are urgently demanding the development of coating devices. In response to these requests, ThreeBond, who has been studying the coating technologies for the past 60 years as a global manufacturer of liquid gasket material, is offering up a solution to our customers for coating devices of liquid materials.
Three Methods of Coating Devices
In general, there are three types of coating devices used for liquid materials and liquid gaskets. Typically, liquid gaskets are applied to the joint surface in points or in lines. Except in very special situations and applications, the coating devices used for liquid gaskets can be classified into three types outlined below.Tracing Method
The tracing method involves feeding gasket material from a reservoir/ or pump through a tube/hose that is delivered to a dispensing valve and then to a nozzle in the form of a continuous bead of material. The nozzle is “traced” by robot or manually along a joint surface to create a solid line of application. Since the process is mountable on an automatic line, this method can be used for various gasket types and applications. Most commonly, the tracing method is used for solvent, aqueous, silicone, or anaerobic liquid gaskets.Screening Method
With the screening method, gasket material is placed on a screen of which area other than patterns to be coated is masked and squeezed on to a joint surface set below the screen through the latter by means of a spatula-like tools (squeegee). Because of its high coating speeds, and high dimensional accuracy of pattern to be coated, it’s a great choice for anaerobic liquid gaskets.Stamping Method
The stamping method uses a box-shaped drum is rotated in a liquid reservoir to form a gasket material film of fixed thickness on its top surface. The film is transferred to a joint surface applied to the top. With high coating speeds that are not limited by complicated geometry or width, it’s a great solution for solvent and aqueous liquid gaskets.Ultimately, ThreeBond offers various types of coating devices for liquid gaskets to ensure you have what you need for every type of application. Our R&D team is hard at work continually refining our solutions to ensure they provide you with the highest quality product that saves you time and money.