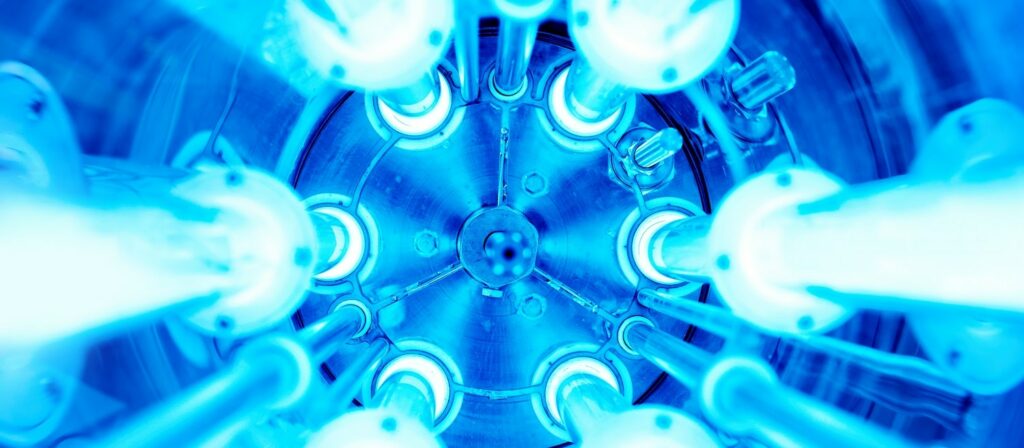
Light Curing Adhesives Compatibility with UV-LED Light Sources: The 3 Things You Should Know
In the past ten or so years, LED (light-emitting diodes) lights have helped move the UV resin industry into a new era. This transition has brought UV resin applications for mobile phones, liquid crystals, and various applications in consumer electronics. Why are LED lights gaining popularity? There are several reasons:
Traditionally, discharge lamps are the conventional choice for light-curing resins, but LEDs have grown in popularity in recent years. Their advantages are numerous, but in general, they can emit light at a wavelength of 365nm. Photo-initiators absorb the light energy and kickstart chemical reactions that polymerize a composite material. Development of UV resins that cure with LED lamps at 365nm has become the baseline for future new product formulation.
These light-curing resins and adhesives are then used as industrial materials for sealing, bonding, and coating.
ThreeBond has developed the TB3017D, TB3017E, and TB3017F mainly for bonding lenses and holders in the electronics market, including optical pickup and camera modules. The product features are:
As the demand for spot curing systems based on UV-LED continues to grow in pickup systems, HDDs, and camera modules, we will continue to innovate new products to accommodate these expanding needs. ThreeBond has continued to provide adhesives suitable for customer systems, and it will continue to strive to serve as an effective partner by developing light-curing adhesives that meet changing needs.
- LEDs provide a longer life
- LEDs offer a lower heat emission
- LEDs provide valuable power savings
1. How Do Light Curing Resins Work?
In most cases, light-curing resins cure instantly when exposed to UV light from a light source. UV light can be used to harden particular glues, resins, and inks. It happens by a photochemical reaction that occurs inside the substances and causes them to harden. This unique trait of light-curing resins and adhesives makes them valuable in the electronics, automotive, and EV and fuel cell manufacturing industries.Traditionally, discharge lamps are the conventional choice for light-curing resins, but LEDs have grown in popularity in recent years. Their advantages are numerous, but in general, they can emit light at a wavelength of 365nm. Photo-initiators absorb the light energy and kickstart chemical reactions that polymerize a composite material. Development of UV resins that cure with LED lamps at 365nm has become the baseline for future new product formulation.
These light-curing resins and adhesives are then used as industrial materials for sealing, bonding, and coating.
2. Why are UV-LED Light Sources Better?
Earlier, we discussed some of the unique advantages of LED lights over traditional lighting sources, but it goes beyond that when it comes to UV-LED lights. UV-LED curing offers significantly lower operating costs when compared to conventional UV curing. There are energy savings involved, fewer consumable parts, and lower maintenance costs. UV LEDs typically use about 30-70% less energy than traditional UV curing.3. Which Light Curing Adhesives are Most Compatible with UV-LED Light Sources?
Developing flexible light-curing resins and adhesives compatible with UV-LED light sources can pose a variety of challenges for conventional technology. Luckily. ThreeBond has already brought several beneficial products to market.ThreeBond has developed the TB3017D, TB3017E, and TB3017F mainly for bonding lenses and holders in the electronics market, including optical pickup and camera modules. The product features are:
- Curable with a UV-LED light source
- Flexible
- Excellent bonding strength
- Excellent environmental durability
- Low halogen products
As the demand for spot curing systems based on UV-LED continues to grow in pickup systems, HDDs, and camera modules, we will continue to innovate new products to accommodate these expanding needs. ThreeBond has continued to provide adhesives suitable for customer systems, and it will continue to strive to serve as an effective partner by developing light-curing adhesives that meet changing needs.